
Blogs
Benefits of Designing Hydraulic Equipment with Hydraulic Cylinders Per ISO Standards
05/08/2017 | Posted by : hydrotonic | No Comments
There are four main ISO standards for mounting dimensions related to hydraulic cylinders. Their nomenclature and other information are listed in Table 1.
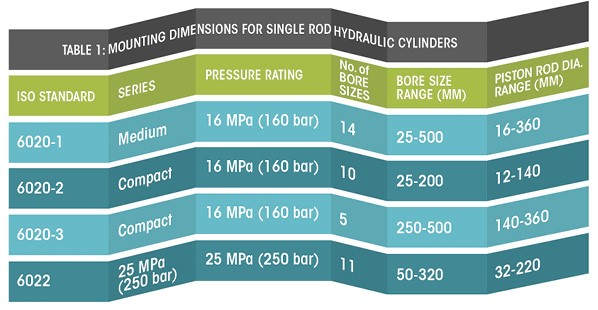
These cylinders are typically available with a selection of two types of threaded ports or a flange-type hydraulic port. Some manufacturers elect to stock some cylinder components in a semi-finished state and machine the ports as specified by customers. Most cylinders are available with a wide range of mounting configurations, with rear-clevis mounts (Fig. 1) or front-flange mounts (Fig. 2) being some of the most popular. Other mounts, such as trunnion, foot, or rear-flange mounts, are also available.
Cylinder structure can be broken down to the pressure envelope section and the piston rod end connection section. The pressure envelope section is normally connected to the machine frame, and the piston rod end is connected to the portion of the machine to which force and motion needs to be applied. This is normally done with a threaded connection on the piston rod end.
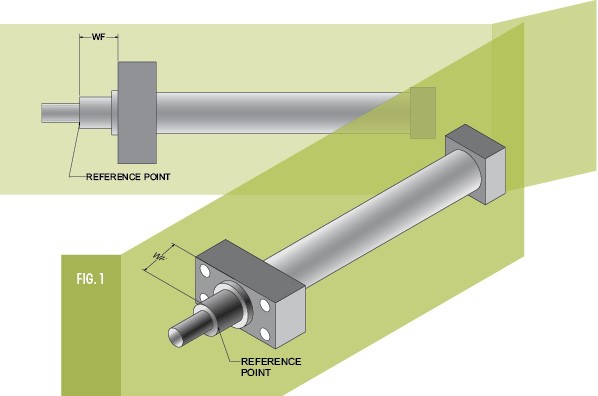
The ISO standards define the maximum overall size of the cylinder envelope, as well as the mounting dimensions with tolerances. In the case of flange mounts, the standards define the flange size, bolt pattern, bolt size, and the dimension to the piston rod connection point. Similar for a rear-clevis mount, the pin diameter, lug size, and dimension to the piston rod connection point is specified. In all cases, mounting dimensions, such as WF and XC (Figs. 1 & 2), are referenced to the shoulder (reference point) of the piston rod with the piston in the retracted position.
ISO hydraulic cylinder standards specify mounting dimensions and overall envelope dimensions only. They do not specify materials, internal construction, or how the different cylinder components fit together. Manufacturers are left free to construct their products as they see fit based on their own manufacturing methods.
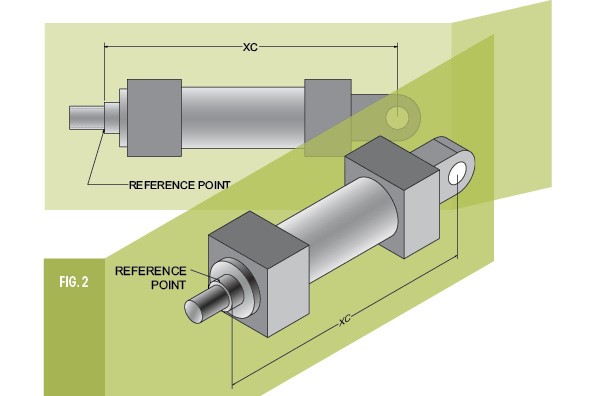
Original Equipment Manufacturers (OEMs) can benefit themselves, as well as their customers or users, when designing hydraulic equipment with hydraulic cylinders built to ISO standards. OEMs normally have preferred vendors. In cases where the preferred vendor is not performing because of quality, price, or work stoppages, an OEM can use another vendor’s product built to the ISO standards without having to make changes to its hydraulic equipment. At times, the end user of the equipment may be in a part of the world a very long way from the original source of the hydraulic equipment and may require a hydraulic cylinder replacement. Parker Hannifin Corp., as well as other manufacturers, can provide hydraulic cylinders built to ISO standards in several parts of the world. The user may be able to locate a local source for the replacement cylinder without going to the original OEM or original cylinder manufacturer.
When a light bulb burns out in our house, we go to the local store and buy a new bulb, not caring where or who manufactured the light fixture or the bulb. We know that we can place the bulb in the light fixture and it will fit and work properly. This is one of the benefits of standardization.