
Blogs
Hydraulic Seal Failures Discussed
Posted by : hydrotonic | No Comments
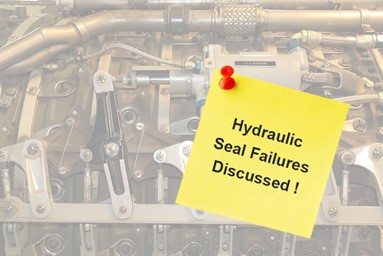
Every hydraulic professional knows, how important are the hydraulic seals in hydraulic systems. Hydraulic seals have a prominent role in eliminating hydraulic leakages and thus by protecting the system from contaminants. When contaminants enter into the system, it can create malfunctioning of hydraulic systems that can lead to a negative impact on the system.
Hydraulic seal failure means that the seal is damaged or defective. It can be because of longtime system operations, mistakes in assembling, inappropriate seal selection, chemical breakdown, contamination, heat erosion and more. There are different types of seals available in the market, that can be used for dedicated applications. In case, if it is selected wrong, the entire hydraulic system will need to face the consequences. The system will leak and causes hazards for workers and workspace. To eliminate such hydraulic system problems, the technician needs to detect hydraulic seal failures immediately and wants to replace that seal with a suitable one.
When a hydraulic seal in any application fails, it can create many issues and some of those issues are listed below.
- Dirt will enter into the system and contaminate the fluid.
- Reduces pressure flexibility. That means, it will inversely affect the low and high-pressure operations of the working system.
- Causes hydraulic system leakages and this will drain fluid in operation. Finally makes the system damaged.
- Leads to fluid blowouts and this uncontrolled release of pressurized hydraulic fluids cause hazards.
- The worn seal material will flow along with the fluid and block the passage. Also, damages system components.
Common Hydraulic Seal Failures
Seal Abrasion: Due to certain mechanical actions like rubbing, scraping and erosion the hydraulic seals start to wear. This is called hydraulic seal abrasion. The reasons for seal abrasion include rough surface finish, damaged or porous surfaces, insufficient lubrication, and contamination.
Seal Extrusion: Existence of gaps between the sliding surface and housing can create failures to hydraulic seals. Under high-pressure, presence of excessive gaps will deform the shape of the hydraulic seal and causes the sealing material to creep or break-off. High system pressure, enlarged extrusion gap, inappropriate sealing material, and cylinder expansion are the common causes for extrusion failures.
Dieseling: The air bubbles present inside the flowing pressurized fluid cause dieseling damages for seals. Under high-pressure, the fumes inside the air bubble will ignite and damages the seal face by burning. Contaminated oil and a sudden increase in pressure are the major reason for dieseling damage.
Hydrolysis: Damages related to hydrolysis causes the break-down of seals. This damage occurs due to the exposure to water and water-based fluids at a higher temperature.
Swelling: Hydraulic fluids that are not compatible with the seals will get absorbed into the seal material and cause swelling. The discolouration of seal and shape deformation by seal loosening are the defects that will be visible. Increased temperature and inappropriate seal selection are the factors that cause swelling.
Side Loading: Extreme sideloads that exceeds the guidance capacity can damage the seals. High temperature and inefficient placing of bushings are the causes of sideloading damage. Sideload will create metal-to-metal contact and results in the breakdown of the system.
Dry Running: Most of the hydraulic seals are constructed with materials that are soft and flexible. These seal materials require proper lubrication for smooth running. Lack of lubrication or dry operating condition will accelerate wear.